With the continuous improvement and development of manufacturing industry, enterprises have higher and higher requirements for efficiency. In the manufacturing workshop, loading and unloading, as one of the most important work of the production line, needs to be operated accurately for many times. However, although the traditional manual loading and unloading method has some advantages, it still has the problems of low accuracy, low efficiency and high labor cost. At the same time, manual operation will also have the operation process is not fixed, difficult to achieve automatic production and other problems, will also pose a threat to the health and safety of operators.
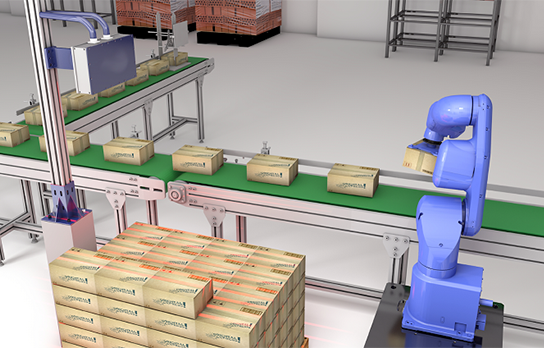
In contrast, robot loading and unloading has the following advantages:
First, high precision
The robot can achieve high precision in the operation process, can more accurately identify, move and place the workpiece, thus reducing the error.
Second, high energy efficiency
Robots do not need rest and sleep and can work continuously, which greatly improves productivity. Compared with the traditional manual operation mode, the robot can complete the same task faster.
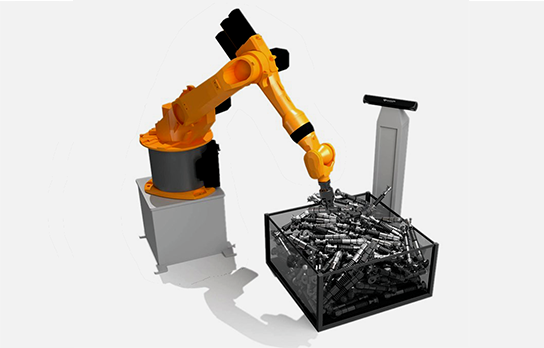
Three, high security
Equipped with a variety of safety sensors and obstacle detection equipment, the robot can operate autonomously without human intervention, thus avoiding accidents caused by human misoperation.
Four, strong scalability
Robots can quickly adapt to the production line process, thus supporting the rapid business expansion of enterprises.
In general, robot loading and unloading technology has become an important trend in the manufacturing industry. It can accelerate the transformation and upgrading of enterprise automation, greatly improve production efficiency and product quality, reduce labor costs and risks, and better meet the market demand. In the future, robot technology will become one of the core technologies for more enterprises to realize digital production in the era of Industry 4.0.