In recent years, with the rapid development of industrial intelligent manufacturing, the visual inspection equipment industry is rising, many enterprises began to introduce a large number of advanced visual inspection technology, so as to replace manual inspection, reduce cost and increase efficiency for enterprises.
However, when choosing visual inspection, many enterprises/factories often fall into the following misunderstandings, resulting in the procurement of equipment and their own needs do not match.
Mistake one test item is fuzzy, demand is not clear
As is known to all, conventional visual testing equipment is divided into inkjet character detection, presence or absence detection, defect detection, appearance detection, size detection, etc. Suppliers will produce visual testing equipment matching the demand according to the daily production needs of enterprises.
Many enterprises are not clear about their positioning and do not know what kind of testing needs they need. They even blindly read a bunch of product defect testing information on the Internet and sort out the requirements of their own product testing items.
Finally, it is found that the equipment purchased back is far from the expected effect, poor experience, heavy losses, and easy to produce disputes.
So how do companies avoid losses?
1. Record defective products during daily manual inspection and conduct classified management;
2. The quality inspection department of the enterprise and the production department should be connected in real time to clarify the testing requirements during production;
3. Provide good samples and bad samples, the equipment supplier will check and test the samples, and feedback the test results.
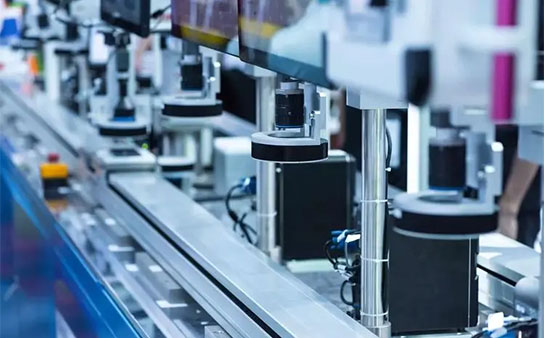
Misconception 2 Visual inspection equipment can be used to detect all products
Many manufacturing enterprises produce a large number of products, not a set of visual inspection equipment can be applied to all products. For example, the same production line of food manufacturers will produce different kinds of food, their outer packaging color, size, pattern and so on are different. In the communication with visual equipment manufacturers, product classification is not carried out, and testing requirements are not determined. In this case, visual equipment manufacturers are unable to give the appropriate detection scheme, which needs to be classified and tested by stages according to the appearance, size, detection items, output and other factors of the product.
Classification of test products and product test items is the key to avoid this misunderstanding.
1. Detection classification: The product is classified into coding detection, size measurement, area detection, surface smoothness detection, hole location detection, etc.
2, specification classification: product size is divided into large, medium and small three parts, according to the shape, size and other classification.
3. Category classification: All products to be tested on the same production line are classified according to the name category.
4. Capacity classification: According to capacity ranking, 1-5 products with the largest output are selected for classification. The greater the capacity, the greater the demand for testing.
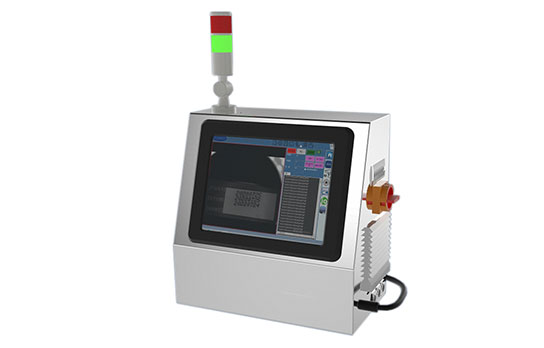
Mistake three set high inspection and acceptance standards, the rate of good products is too low
Manufacturing enterprises do not establish acceptance standards and testing requirements according to the actual products produced by the enterprise, but adopt industrial standards or theoretical standards to establish testing item standards.
Finally, the equipment is customized according to the requirements, but after the delivery of on-site use, their own production rate is low, so that the machine detection is not accurate enough, and finally require visual manufacturers to transform.
How to avoid high testing standards?
1. According to the ordering and acceptance standards of enterprises, formulate acceptance standards for visual testing equipment;
2. According to the quality inspection data and the actual quality inspection standards, formulate the corresponding machine vision inspection equipment standards;
3. Appropriately increase testing items, improve testing standards, improve product quality, and enhance product market competitiveness.
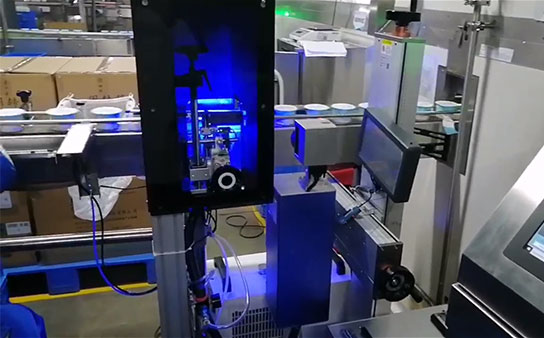
Misconception four foreign brand is better
Foreign-funded enterprises are mainly divided into two types:
One is that the global scale and strength are relatively large, established earlier, but their visual products are often single function, it is difficult to meet the ever-changing testing needs of China's manufacturing industry, machine vision products purchased back can not fully meet their needs, the price is high and impractical.
There is also a foreign enterprise itself is a local enterprise, registered in a foreign company, transformed into a foreign brand enterprise, this kind of enterprise often pay attention to brand packaging, lack of core technology, difficult to guarantee after-sales.
How to choose a suitable visual inspection system supplier?
1. Look for the manufacturers of visual inspection system, send samples for testing, comprehensively evaluate the compatibility between the two parties, and then go to the manufacturers for field visits;
2. Inspect whether visual suppliers have relevant strength, independent research and development, agents, service reputation, etc.;
3. How about the compatibility and expansibility of the visual software and equipment? Because with the development and adjustment of the company's business, the project currently tested may need to be improved in the future, and the software must be universal for the later detection of other products.
Visual inspection equipment instead of manual inspection, the transformation of industrial quality inspection method is the inevitable choice of industrial upgrading.
Manufacturing enterprises in the selection of machine vision testing equipment, first of all to understand their own needs, in order to better choose their own enterprise product testing equipment, at the same time to choose a good market reputation, visual testing equipment manufacturing project experience of rich enterprises, so as to have better product quality assurance, and after-sales service protection.
Fuwei Intelligent focuses on the research and development, production, sales and service of machine vision, intelligent robot and flexible equipment. With many years of experience in field application, Fuwei Intelligent can provide perfect solutions to help customers achieve efficient and high-quality production.