Laminated steel wire hose is a kind of laminated steel wire reinforced hose specially used in the automotive field, which is mainly used in the hydraulic system, fuel transmission pipeline, cooling system, braking system and other aspects of various vehicles. On the production line, the incoming material of the hose is placed in the basket in a disorderly manner, and the position, direction and height of each hose are not the same. This makes the traditional fixed-point robot grasping method difficult to grasp. The traditional grasping method needs to show and teach the fixed point, which requires higher consistency of incoming materials. The 3D vision guide hose grabs the loading and unloading materials in disorder, and accurately positions the workpiece through vision, which can greatly improve production efficiency, achieve flexible production, and reduce personnel damage and misoperation.
Based on a large number of customer project requirements and application practice, Fuwei intelligent has accumulated a wealth of technology, solutions and application experience in the rubber hose workpiece loading and unloading scenario. Automatic loading and unloading of rubber hoses through AI+3D technology helps end customers improve production efficiency and quality and create flexible production solutions.
Solution | 3D vision guide hose grab and load materials in disorder
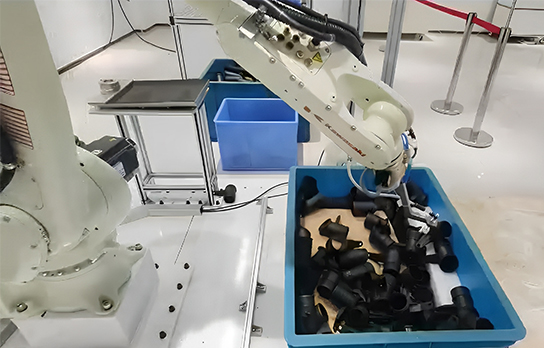
Project Overview:
The hose is placed in the material frame in a disordered manner, 3D vision identifies and locates the workpiece, guides the robot to grasp and load the hose in a disordered manner, replaces the manual with a mechanical arm, and the grasping accuracy is ±0.25mm, which can run stably for 24 hours.
Technical difficulties:
1, the workpiece is pure black, has a greater impact on the camera point cloud imaging;
2, high accuracy requirements, accuracy requirements ±0.25mm;
3. The incoming material is in disordered state, requiring secondary positioning;
4, a single robot is responsible for the workpiece loading and unloading of two stations.
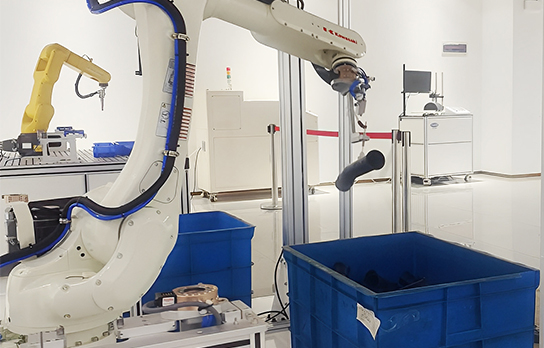
Solution:
1, the use of multiple exposure point cloud superposition to ensure the quality of the workpiece point cloud;
2, using self-developed high-precision 3D visual positioning algorithm, workpiece positioning accuracy of ±0.25mm;
3, using deep learning and hardware acceleration algorithm to improve the tempo;
4. It can adapt to the scene of simultaneous production of multiple workpieces.
The combination of robots, 3D vision systems and AI algorithms allows robots to handle materials in a more accurate and stable manner, greatly improving production efficiency. The use of 3D visual guidance technology can achieve accurate identification and positioning of items, so as to help the robot quickly and accurately grasp the item, and place it in the designated position to achieve automatic sorting and loading and unloading of the workpiece.
3D vision guided hose random grab and loading is a classic application in the field of intelligent robot application, and it is also a successful application of robot technology in the field of production. In the future, with the continuous innovation and intelligence of robot technology, it is believed that more fields can apply intelligent robot technology to bring more convenience and efficiency to our production and life.