Summary:
The vision guided robot grabs high-precision 3D workpieces in disorder and assembles the workpieces at the specified position as required. | 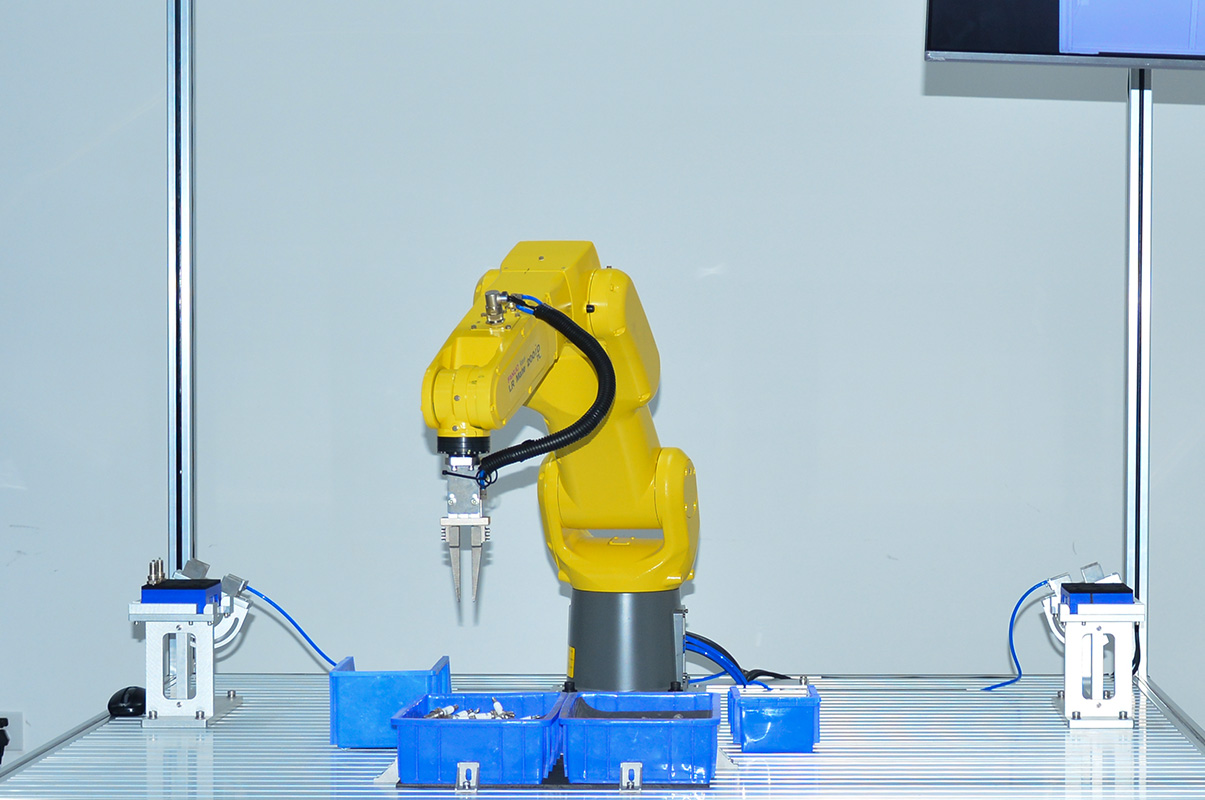
|
Case background
Spark plugs and screws are placed disorderly in the material frame. They are selected through manual packaging. The need to turn over is confirmed according to the front and back of the workpiece. It is entirely manual. The labor intensity of workers is high, and the cost is high. Therefore, automatic transformation is required
Technical difficulties
1. The workstation is located at the entrance of the plant, and the light changes greatly in the morning and evening;
2. The incoming materials are out of order and difficult to load;
3. Multiple products are produced at the same time, and the automation equipment cannot be adapted;
Core advantages
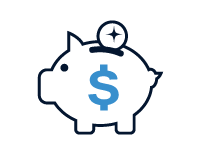
High intelligence Large field of view, large depth of field, easy integration
| 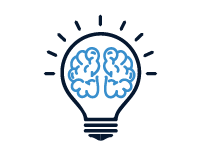
Multi function selection | 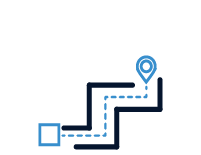
High intelligence |
Solution
01. The vision part adopts 3D structured light camera+depth learning algorithm.
02. 3D vision is used to locate the products in the material frame to avoid collision points and generate grab points.
03. 2D vision is used for accurate positioning twice to ensure the accuracy of feeding.
04. Set multiple grabbing points for the workpiece to improve the frame clearing rate.