Outlined:
The composite robot uses 3D vision to guide the robotic arm to grab the work fixture from the fixture library, place it on the storage rack, and then the composite robot transfers it to the line body, thus using 3D vision for positioning guidance to place the fixture on the line body station. It can be applied to the workpiece transfer loading process in 3C, pharmaceuticals, steel and other fields.
| 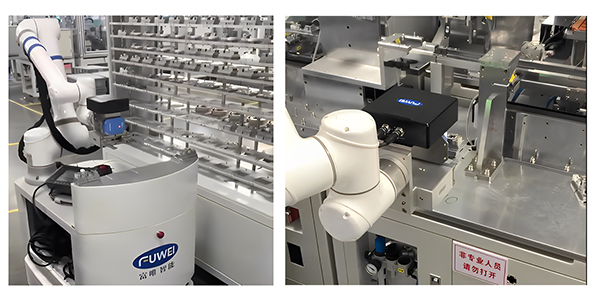 |
Case background
The customer is a national high-tech enterprise focusing on the research, development, production and sales of connectors, the products are mainly used in aerospace, military, automotive and communications and other fields. When changing products, it is necessary to manually take more than 40 pieces of fixtures and carriers from the fixture library to the fixed position of the wire body, which is time-consuming and error-prone.
Technical difficulties
1. Complex factory environment with large changes in light.
2. a large number of jigs and fixtures, and can not meet the production line flexibility requirements.
3. Need to quickly compatible with a variety of products, traditional non-standard automation equipment can not be achieved;
4. High precision requirements, pin precision within 2MM.
5. There are many kinds of jigs and fixtures with different sizes.
Prescription
1. 3D vision compensation is adopted at the end of the machine arm, and the 3D vision positioning accuracy can reach ±2mm.
2. 3D structured light camera is adopted to achieve highly flexible automated production.
3. composite robot with laser slam navigation technology parking positioning accuracy ±5mm;
4. automatic charging technology, composite mobile robot below the set value can be automatically charged to meet the user 7x24 hours uninterrupted work.