In recent years, with the continuous expansion of urban scale, urban traffic congestion is prominent, more and more people choose urban rail transit as a daily travel tool. However, the speed of urban rail transit vehicles continues to improve, the carrying weight of trains and the density of vehicles continue to increase, which puts forward higher requirements for the stability, safety and maintenance of rail transit auxiliary equipment.
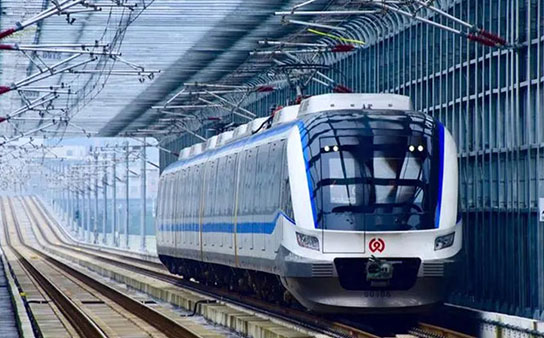
As the key equipment of switch switch, any failure will make the train unable to operate normally, and may even cause the train to fall off the rail, roll over and other serious consequences, resulting in serious loss of life and property. Therefore, the importance of railway switch machine is self-evident, manual handling of loading is difficult, high risk, how to use artificial intelligence technology instead of human labor for railway switch machine positioning grab loading, is an urgent need to be solved by railway Bureau.
A railway bureau railway switch machine visual high precision positioning grab
Project background:
Railway switch machine is heavy in weight and large in volume. If the traditional manual loading is carried out, the work intensity is very high, and multiple workers need to be deployed for repeated handling. In the process of moving back and forth, the switch machine is prone to knock, resulting in industrial injury risks for workers and increasing labor costs. In order to reduce costs and increase efficiency, the customer hopes to improve through automation.
Difficult points of the project:
1. The incoming state of the workbench is disordered, the size and volume of the workpiece are large, and it is difficult to shoot the whole workpiece with a single camera;
2. The back-end docking assembly process requires higher accuracy of workpiece positioning, and the surface reflection increases the difficulty of image recognition and positioning.
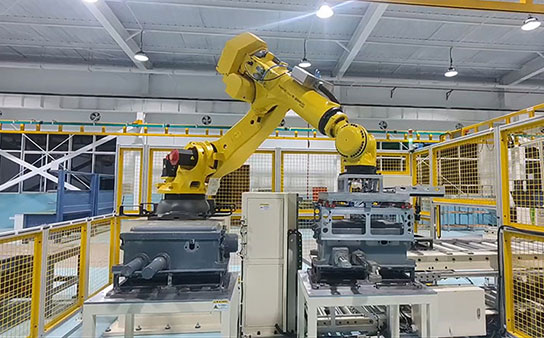
Solution:
1. Accurate positioning of the workpiece was completed by using 2D visual multi-photo point data fusion algorithm. Different positions of the workpiece surface were photographed by monocular camera to accurately locate the part;
2. Independently developed high-precision calibration algorithm of multi-point camera, integrated data of different photo positions, and finally realized accurate positioning of the whole workpiece;
3. Finally, according to the hand-eye calibration results, the coordinates are transformed into the robot coordinate system, and sent to the robot to complete the workpiece grasp through TCP communication.
Advantages of the scheme:
1, instead of manual, high-precision 2D visual positioning of large parts, not only to ensure high accuracy and reduce costs;
2. Self-developed multi-point data fusion algorithm, independently developed trajectory planning algorithm of intelligent robot arm, capturing success rate up to 99%;
3. The system can run stably for 24 hours.
The railway bureau introduced the Fuwei intelligent high-precision visual positioning grasping system to capture and feed the railway switch machine. The precise positioning was carried out through 2D vision, and the precise positioning coordinates were provided to the robot, which greatly improved the automation and flexibility level of the production line and guaranteed the accuracy and safety of the feeding.
Based on customers' actual scenario requirements, Fuwei Intelligent can provide powerful, flexible and easy-to-use visual high-precision positioning grab loading and unloading solutions. After simple debugging and training, the required functions can be quickly realized, helping the majority of integrators deliver smoothly, and helping customers achieve efficient and high-quality production.